Essential Guide to Chemical Injection Pump Maintenance: Maximizing Performance and Longevity in Industrial Applications
Chemical injection pumps are the backbone of precise chemical dosing across countless industrial operations, from water treatment to oil and gas processing. When properly maintained, these critical pieces of equipment can deliver accurate metering for years – but neglect can lead to catastrophic failures and costly downtime. At MJ Systems, we’ve spent decades perfecting custom-engineered solutions for the most challenging chemical injection applications, and we’ve learned that proper maintenance isn’t just important – it’s essential for operational success.
Whether you’re managing diaphragm pumps handling corrosive chemicals or metering pumps delivering precise dosages onshore or off, our comprehensive engineering support team has seen it all. We understand that every application has unique maintenance requirements, especially when dealing with hazardous materials, high viscosity fluids, or extreme operating conditions. Our approach combines proven industry best practices with specialized knowledge of complex chemical handling systems to ensure maximum uptime and reliable performance.
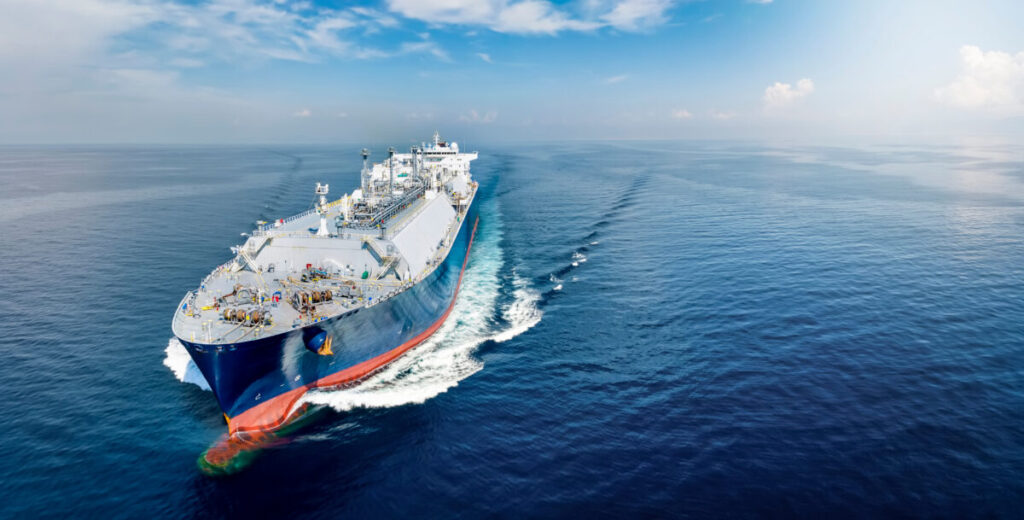
The Critical Importance of Chemical Pump Maintenance for Industrial Operations
About 80 percent of maintenance mistakes involve human factors, which is why establishing a systematic maintenance approach is crucial for chemical injection systems. Proper maintenance not only prevents equipment failure, reduces operating expenses, increases the longevity of equipment as well as ensuring your facility remains compliant with environmental regulations and safety standards.
In industries where precision is paramount, consistent maintenance translates directly to improved product quality and operational efficiency. When chemical injection pumps fail, the consequences can be severe – from environmental contamination to production halts that cost thousands of dollars per hour. This is why MJ Systems emphasizes the importance of proactive maintenance strategies that address potential issues before they become critical failures.
Developing Your Chemical Pump Maintenance Schedule
The foundation of effective pump maintenance is establishing the right service frequency. While industry standards typically recommend quarterly maintenance for most chemical injection pumps, your specific schedule should account for several critical factors including operating conditions, chemical properties, flow rates, manufacturer guidelines, and regulatory compliance requirements.
Your maintenance program should include regular visual inspections for leaks, corrosion, or unusual deposits, along with examination of seals, gaskets, and O-rings. Performance monitoring is equally important – verify dosing accuracy and flow rates, monitor pressure readings and trends, and check electrical connections and controls. Don’t forget to regularly inspect lubricant levels and condition, checking bearing temperatures and vibration patterns.
Best Practices for Chemical Pump Maintenance
One of the most critical aspects of chemical pump maintenance is ensuring proper material compatibility. As specialists in custom-engineered solutions, we emphasize that failure to consider the fluid and its concentration when specifying a pump can result in severe damage and premature failure. Always verify material compatibility across the entire system, including wetted parts and components, seals and gaskets, piping and fittings, and consider chemical concentration and temperature effects.
Common maintenance mistakes include ignoring early warning signs like increased vibration, using non-compatible replacement parts, improper calibration procedures, inadequate documentation of maintenance activities, and delaying scheduled service intervals. These errors can lead to significant operational problems and should be avoided through proper training and adherence to maintenance protocols.
Advanced Maintenance Strategies
Modern technology offers numerous opportunities to enhance your maintenance program. Implementing IoT monitoring enables real-time performance tracking, while predictive maintenance technologies can identify potential issues before they cause failures. Regular flow verification tests ensure accuracy, while monitoring chemical consumption patterns helps optimize dosing efficiency. Annual system audits provide comprehensive evaluation of overall performance and identify areas for improvement.
Spare parts management is crucial for minimizing downtime. Maintain a critical spare parts inventory based on usage patterns, stock wear items appropriately, and keep manufacturer-approved components readily available. Replace high-wear items proactively to prevent unexpected failures.
MJ Systems’ Approach to Chemical Pump Maintenance
As a leader in custom-engineered metering solutions, MJ Systems provides comprehensive support for maintaining your chemical injection equipment. Our expert engineering team offers front-end design consultation, material selection guidance, spares stocking and interchangeability recommendations, troubleshooting assistance, and performance optimization. We provide specialized training programs covering pump theory, accessory equipment, operator techniques, maintenance best practices and safety procedures.
Partner with MJ Systems for Maintenance Excellence
Don’t let maintenance challenges compromise your chemical injection operations. At MJ Systems, we combine decades of expertise with innovative solutions to keep your systems running at peak performance. Our team of engineers understands the unique requirements of critical chemical handling applications and can develop a maintenance program tailored to your specific needs.
Ready to optimize your chemical injection pump maintenance? Contact MJ Systems today for expert engineering support and comprehensive maintenance solutions. Let us help you implement a maintenance program that maximizes uptime, ensures safety, and delivers reliable chemical dosing performance for years to come.
Contact our experts now or visit our website to schedule a consultation and discover how our proven maintenance strategies can benefit your operation.