Is Your Pump Old Enough to Drink? The Case for Modernizing Chemical Injection Pumps, Part II
The industrial landscape is constantly evolving. New chemicals, changing processes, and advancements in automation require that your chemical injection pumps are up to the task. Modernizing your pumps is essential to keep pace with these changes and ensure that your operations remain safe, efficient, and reliable.
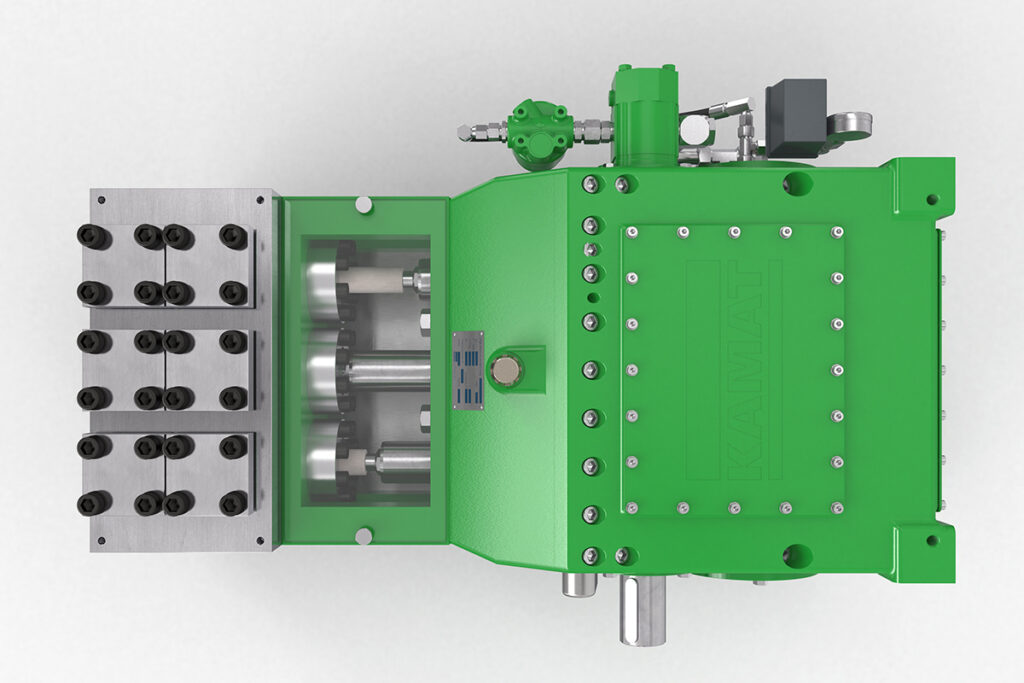
Process/Application Changes
Oil & Gas application requirements often change as production throughput increases or decreases, as a result of aging wells or prescribed production outputs by the owner/operator. Chemical manufacturers also alter chemical recipes, expand production environments, alter product capacity, and employ procedural changes. Upon application modifications, making certain that the chemical pumps and systems are best-fit and capable of delivering process chemicals in an effective and safe manner is imperative.
- Chemical Changes/Modifications: Process chemical compositions can change for a given application as can the recipes that utilize said chemicals. It is crucial to ensure that the materials of construction for the pump and system “wetted” components are fully compatible with the process chemicals. Often, a simple component materials change is sufficient if all other operational requirements remain the same.
- Process Condition Changes: For various reasons, process conditions can change for a specific application. The obvious variables to account for are any changes in suction pressure, discharge pressure, chemical viscosity, temperatures (process or ambient), and flowrates. Process condition changes require immediate attention as failure to do so can result in immediate or catastrophic failure regarding the product quality and system components.
Automation/Integration
The automation and direct integration of chemical pumps to the process control system is becoming commonplace. Advancements in automation are leading to safer process environments while improving production output and product quality. Modernizing pump system assets with “automation-ready” components and accessories enables advanced monitoring and control of system conditions, pump status/performance, data trending, etc. Furthermore, today’s automation systems are helping mitigate the human error factor and keeping personnel distanced from hazardous environments.
- Flow Control Method: Rather than local manual flowrate adjustment, pump systems are being fitted with automation devices and accessories to remotely monitor the pump system metrics and control the operation of the pump and other devices in the flow-stream. Often, pumps can be modernized by retrofitting manually operated models with automation devices and accessories. An example is the use of an electric stroke length adjuster which utilizes a control signal (4-20mA or 0-10v) to change the stroke length of the pump, which alters the flowrate.
- Flow Control Philosophy: Smart or active pump control systems are being utilized at an accelerated rate. These types of pump systems can be programmed to autonomously adjust their flow rate per real-time system conditions feedback. If the pump system is equipped with the automation-ready components mentioned earlier, the pump can be controlled and monitored via the control system, regardless of the type of flow control program being utilized by the DCS or PLC.
Modernizing your chemical injection pumps is not just about keeping up with the latest technology; it’s about adapting to the ever-changing needs of your industry. By investing in pump modernization, you ensure that your operations remain compatible with new chemicals, processes, and automation technologies. This proactive approach not only improves efficiency and safety but also allows you to embrace new opportunities and maintain a competitive edge in the marketplace.
Ready to modernize your chemical injection systems?
MJ Systems specializes in delivering proven, custom-engineered solutions for your metering, dosing, and chemical injection applications. We offer comprehensive support from front-end design to installation, training, and aftermarket support. Contact us today to learn how we can help you optimize your processes and achieve your production goals.