What Are the Most Effective Industrial Applications of Chemical Injection Technology?
Optimizing Process Efficiency Through Strategic Chemical Dosing Systems
At MJ Systems, we’ve spent over two decades at the forefront of chemical injection technology, designing and implementing precision dosing solutions for some of the most demanding industrial environments worldwide. Our team of factory trained engineers possess a unique combination of theoretical knowledge and practical field experience to every project, allowing us to address flowline challenges that standard off-the-shelf systems simply cannot solve. Unlike providers who merely supply equipment, our engineers partner closely with our clients throughout the entire process—from front end engineering, through system design, installation, ongoing maintenance and training. This consultative approach has established us as trusted advisors to facility managers, reliability engineers, maintenance and operations personnel across most major oil and gas, chemical and petrochemical producers. Our clients consistently report reduced chemical consumption, improved process reliability, and significant cost savings after implementing our custom injection solutions. We take pride in developing solutions that not only solve immediate operational challenges but also adapt to evolving production demands and process requirements.
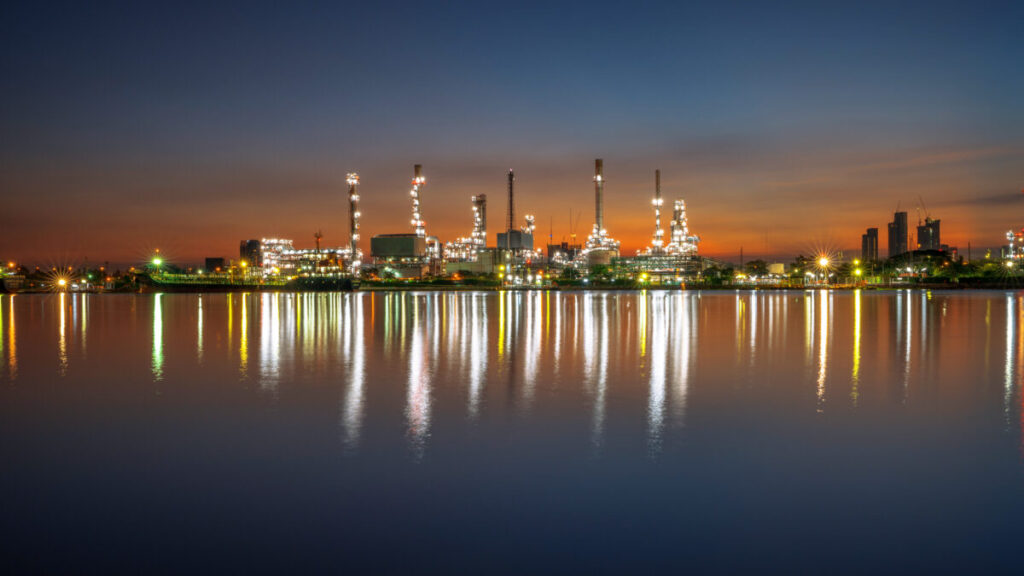
Oil and Gas: Precision Chemical Management for Critical Operations
In the high-stakes environment of oil and gas production, chemical injection systems play a pivotal role in maintaining operational safety, integrity and efficiency.
Flow Assurance and Asset Protection
One of the most critical applications in this these sectors involves preventing paraffin and scale buildup in pipelines and production equipment. Our chemical injection systems deliver precise amounts of inhibitors at strategic points throughout production infrastructure, preventing the costly downtime associated with cleaning and maintenance operations. A major producer in the Gulf Coast region recently reported a 78% reduction in unplanned maintenance interventions after implementing our adaptive injection technology.
Corrosion prevention represents another crucial application, particularly in environments with high H₂S or CO₂ content. Our systems maintain optimal corrosion inhibitor concentrations despite fluctuating production rates and fluid compositions, extending equipment life and preventing catastrophic failures. This adaptive approach has proven particularly valuable for operations in the variable production environments common in shale plays throughout the Southwest.
Production Optimization and Separation Efficiency
Chemical demulsifiers play a crucial role in separating oil and water during processing. Our injection systems provide precise dosing that adjusts automatically to changes in production fluid characteristics, optimizing separation efficiency while minimizing chemical usage. This precision becomes particularly important when processing heavy crude oils or handling production from mature fields where water content fluctuates significantly.
The natural gas sector benefits from our methanol injection systems, which prevent hydrate formation in pipelines during cold weather operations. Regional clients operating in the Mountain West have reported substantial savings by utilizing our weather-responsive control systems, which adjust methanol injection rates based on real-time temperature and pressure conditions rather than fixed schedules.
Water and Wastewater Treatment: Balancing Compliance and Cost-Effectiveness
The water treatment sector faces dual pressures: meeting increasingly stringent regulatory requirements while controlling operational costs.
Industrial Wastewater Processing
Manufacturing facilities face increasing pressure to treat process wastewater to higher standards before discharge. Our pH adjustment systems provide responsive control through proportional injection technologies that prevent the oscillation common with simpler on/off systems. This precision is particularly valuable for facilities processing variable waste streams with fluctuating chemical characteristics.
Metal finishing operations benefit from our flocculant and coagulant injection systems, which adapt to changes in wastewater turbidity and metal content in real-time. These systems have helped numerous facilities in industrial parks across the region achieve consistent compliance with discharge permits while minimizing chemical consumption.
Ready to Optimize Your Chemical Injection Processes? Contact MJ Systems Today!
Don’t let imprecise chemical management compromise your operational efficiency, product quality, or safety. At MJ Systems, we specialize in designing custom chemical injection solutions that address your specific industry challenges while providing measurable return on investment.
Contact us today to schedule your consultation, or visit our technology center to see our latest injection systems in action. Let’s work together to transform your chemical processes from a necessary expense into a competitive advantage.