Drag Reducing Agent Injection Solutions
The Drag Reducing Agent Injection Challenge
Drag reducing agent injection presents a challenge particularly when selecting the key component solutions. The characteristics of drag reducing agents (DRA) make it a notoriously difficult injection application to pump and meter. The shear thickening long-chain polymers tend to drop out of suspension in the carrier fluid causing solids to coagulate if not adequately agitated. Our experience in metering critical fluid mediums also informed our decision to shy away from positive displacement flow meters in this type of application due to the potential that shearing would likely clog the instrument. With these facts in mind, read below to see how we solved this tricky DRA application.
DRA Application Details
A major offshore oil & gas producer in the Gulf of Mexico approached MJ Systems (MJS) engineers with their problem DRA application. The end user needed to treat their pipeline with DRA to reduce turbulence in the pipeline and enhance oil flow. The pipeline ran from the offshore facility back to shore. Our engineer recommended the Graco Python XL DA pneumatic pump solution and invited the customer’s engineers to a witness test in our shop. Due to several prior pump failures in this application, the company’s facilities engineer wanted to see the test with their ChampionX DRA fluid at the operating flow/pressure of 5 GPH at 1,200PSI.
Key DRA Equipment Solutions

The Graco Python XL DA pump offers a unique feature, positive suction. In other tests, our engineers witnessed the unit successfully pumping peanut butter and honey so our team knew the pump could overcome the viscous properties of DRA fluid. During the customer test, the bucket of DRA sat at ground level with the pump mounted 4 feet above it. This reduces NPSHA. The positive suction forces inherent to the pump design results in a negative NPSH required. In fact, when the Graco factory originally tested the unit in development, it pulled water through a hose from a base elevation to the top of their 30 foot high manufacturing facility!
The MJS engineers also recommended Rheonik Coriolis meters for several reasons. The sealless, thick walled, dual tube construction matches the pipe specification and would not break the long chain polymers in the fluid. The no-moving-parts design meant little to no maintenance for the customer’s maintenance teams. The meters achieve pressures above 23,000 PSI, well within the range of the operating conditions. Plus, coriolis meters accurately read low flow rates.
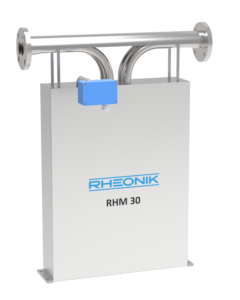
Results

The successful demonstration of Graco’s ability to pump viscous fluids with negative suction pressure resulted in the complete injection skid award. Later, when the flow rate of the application changed mid-fabrication, the versatility of Rheonik and Graco accommodated the change without a change to the equipment. The MJ Systems’ market expertise allowed our teams to source all other major components whether on or off line sheet. Because MJS works with multiple fabricators, we selected one with the know-how to build a functional chemical injection skid suited to the demanding specifications for offshore installations. Contact our team of experienced engineers to solve your flow line’s challenges!