Whether the issue is related to normal wear and tear, process changes, conditions around the pump or something more, MJ Systems will identify a solution. We know these pumps serve the most critical parts of your process, the virtually limitless cost of halted production and the value of minimized downtime. In nearly all cases, our customers return to smooth operation for a fraction of the cost and time of full replacement.
MJ Systems, In-House Service Capabilities for SPX Flow>Bran+Luebbe
With more than 25 years of experience with SPX Flow>Bran+Luebbe equipment, you can rely on the expert technicians at MJ Systems when your B+L pump requires routine maintenance and repair.
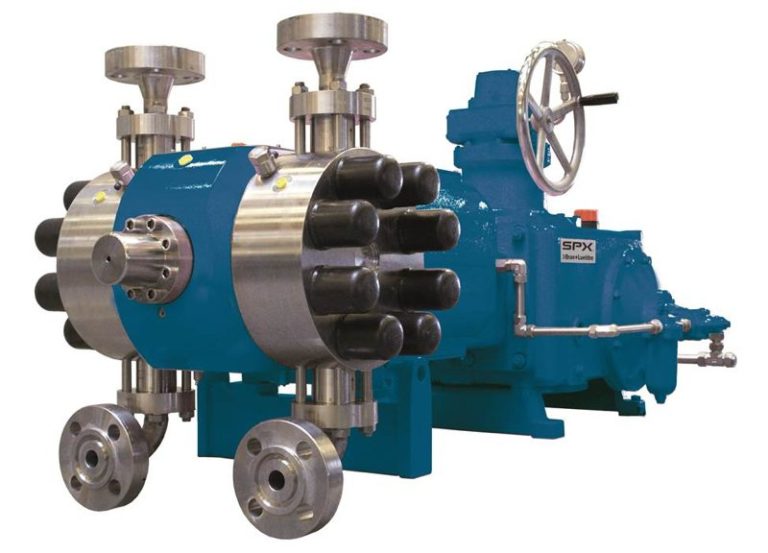
Maintenance Procedures
- Inspection: Verify decontamination complete. Review MSDS sheets.
- Teardown: Disassemble pump to evaluate repair need and work scope.
- Approval: Quotes for approval are usually generated within 5 business days.
- Clean: All components washed and debris removed
- Parts Replacement: Re-assemble pump and/or gear box and install/replace required parts.
- Performance Testing: Ensure the unit is operating correctly.
- Paint: Pumps/gearboxes are painted to specification as needed.
- Report: Issue a service report
SPX Flow>Bran+Luebbe Factory Field Service
A trained SPX Flow factory technician perform equipment evaluations, upgrades, retrofits, maintenance and repair of your Bran+Luebbe equipment to include an OEM guarantee / warranty for all service work. Authorized field service is available to both onshore and offshore end users.
SPX Flow>Waukesha Cherry-Burrell In-House and Factory Service
Our shop will clean and replace parts, rotors, bearings shafts and seals Waukesha Cherry-Burrell units. For advanced repairs requiring machining capabilities, units may be sent to the factory in Delavan.
KAMAT Simplified Service
One of the most advantageous features of the KAMAT design is serviceability. Designed with service in mind, the KAMAT pump may be serviced by low skilled workers due to the limited number of parts required to affect repair. Technicians may access all wearing components for a head repair through a cover on the intermediate chamber without removing the pump head. Perform gearbox repairs without draining the oil. Our team of experts support repair requests for these units in the field or in our shop.
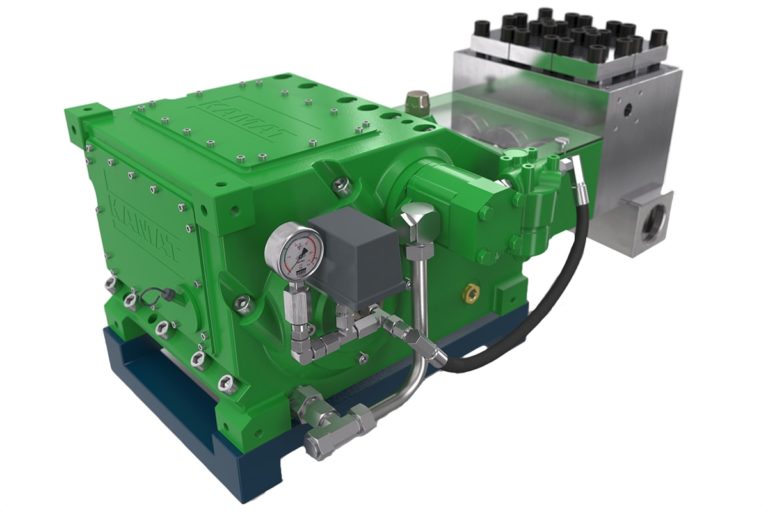
Graco Serviceability
As a stocking distributor of Graco oil and natural gas chemical injection equipment, our team of experienced technicians are available to provide trouble shooting support by phone, in the field or in our shop. For most issues, the Graco line is easily serviceable in the field.
CheckPoint Factory Service
CheckPoint is committed to being a good partner for the entire life cycle of the product. In addition to technical support, CheckPoint will provide all documentation, maintenance and troubleshooting information required to ensure that your pumping system is fully operational and functioning effectively.